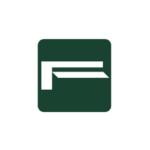
Electric Heating
Welcome to Electric Heating: The Energy Efficiency Podcast – episode 6, the podcast that brings you a mix of energy efficiency news, products and tips all year round. We’re interested in profiling people and products involved in promoting energy efficiency habits, products and information, so please do get in touch if you have something to contribute.
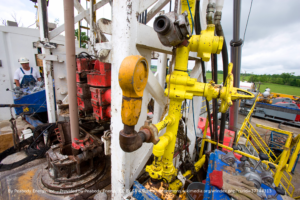
Before we get on with our advertised features, we looked recently at the role of carbon capture in helping the UK achieve Theresa May’s net zero target. Carbon capture traps carbon as it’s produced, preventing it entering the atmosphere. The carbon can then be used to create chemicals required by industries including food (mm) and medicine. Last week, a division of the Indian-owned company Tata announced a new carbon capture project, the UK’s biggest, through a plant in Cheshire. It expects to prevent 40,000 tonnes of carbon entering the atmosphere each year, the equivalent of removing about 20,000 cars (what type of cars?) from the roads.
The plans are backed by the British government, which is contributing about a quarter of the £16m cost through a grant. An existing carbon capture trial at the Drax power plant in Yorkshire will receive a £5m boost, aimed at keeping 16m tonnes of carbon from the air by the mid-2020s. The government is helping to support nine carbon capture projects and supporting the development of a net zero industrial cluster in the UK by 2040.
The Tata project intends to use the removed carbon to create a high grade liquid carbon dioxide, used in creating baking soda. Sodium bicarbonate is used by pharmaceutical companies to make products including indigestion remedies and eye drops. Tata is the only company in the UK making sodium carbonate, which is used in detergent and glass manufacture. As Martin Ashcroft, head of Tata Chemicals Europe, points out, this carbon capture project helps Tata ensure a good supply of essential materials.
Tata is an enormous company with interests in many sectors. It owns one of India’s biggest energy companies, and has pledged to end investment in fossil fuel energy plants to focus on renewables instead. Realistically, it is behemoths such as Tata that have the influence and financial muscle to make changes the ordinary person can’t effect, so let’s hope that where Tata leads, on these issues at least, others will follow.
—
Electric heating
Last week we looked at gas heating, concluding that although it is cheaper per unit than electric heating and emits less CO2 than almost any other form of heating, it’s expensive and disruptive to install, an inherently risky material and, of course, a fossil fuel. Much natural gas production comes from fracking, particularly in the USA, which is widely accepted to be an environmental disaster.
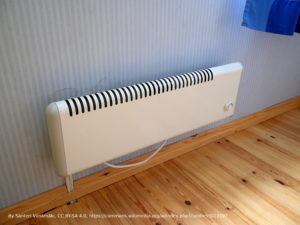
In the UK, many houses that aren’t connected to the gas network instead use electric heating. About 4m households here don’t have access to gas, and of these about half use electric heating, so at two million households that’s a noticeable minority. Of these two million or so households, the vast majority use night storage heaters with the rest using plug-in fan heaters. A small minority of less than 100,000 households use heat pumps, which need electricity to run but are a whole subject in their own right and will be profiled next week.
Is it really more expensive?
Electric heating is more common in flats than houses, and homes using it tend to have a lower energy efficiency rating with the occupants on lower incomes, directly leading to fuel poverty. A report from Ofgem, Insights Paper on Households with Electric and Other Non-Gas heating, goes into deep but quite interesting detail on the demographics of electric heating customers, and how things will probably become worse for them financially over the next few years as tariffs and benefits become unbalanced and these customers are poorly-placed to take advantage of the best deals.
Electric heating is more expensive on a per-unit basis than gas, but installation is much simpler as pipework isn’t needed for a standard system with wall-mounted heaters. It’s straightforward to use or replace only part of the system. There is a reduced requirement for annual checks and maintenance, although not necessarily in high rise buildings and the rules are different on unvented electrical hot water systems, so an electric heating system can significantly outlast gas or oil systems. Given that effectively all houses in the UK have an electricity supply as standard, those paying the standing charge for gas on top have an extra charge.
Looked at as a whole over its lifetime, electric heating does not necessarily leap out as dramatically more expensive than gas or oil, but this might well feel different if you have inherited a system and/or are a tenant who is stuck with high electricity heating costs but doesn’t see the direct benefit of reduced installation costs and a longer system life.
Storage heaters
All electric heating is not equal. Most electric heating customers will have either night storage heaters, or controllable central heating. Night storage heaters, also known as electric storage heaters or just storage heaters, do what it sounds like they do – they store heat to disseminate later. Often this heat is built up during cheaper tariff hours, commonly overnight. This requires a particular circuit and meter, and the cheaper hours are dictated by the power provider. As the heat builds up in an element in the heater, it’s absorbed by high density material.
Standard models of storage heaters gradually release heat during the day, but there are smart fan-driven systems that retain nearly all the heat until it’s needed. Newer automatic and more efficient models absorb heat depending on the temperature of the room, and combination models can top up during the day using peak rate energy, if necessary. Since I last used storage heaters 17 years ago, the storage and control has improved from the already rather old clunky units that were hot when I didn’t want it, and cold when I wanted heat. Older heaters have a tendency to collect dust and dirt in their filters and fans.
Since January 2018 new storage heaters must comply with the European Ecodesign Directive, requiring them to meet a minimum energy efficiency of 38% for a heat output above 250W. This is in part what has driven improvements to storage heater design. The Ofgem report states that a proportion of night storage heater customers don’t feel warm enough. Together with complex bills easy to misread, and faulty equipment using too much power or producing too little heat, there are many complaints from electric heating customers.
Perhaps storage heaters are a useful addition to standard gas, electric heating or oil heating in a non-standard domestic set-up, eg a multi-phase building that doesn’t have central heating or gas heating fitted throughout. It could also present a cost-effective way of managing different warmth requirements, eg if someone ill or elderly wants their room warmer than the rest of the house finds comfortable, but without running an expensive fan heater. Ultimately the pro of storage heaters is that they are lower cost to run, drawing energy during off-peak hours. Basic models can still make a room uncomfortably warm, and it’s easy for all the heat to be used up by the evening.
Direct Acting Electric Heating Systems offer another option, and work well in properly-insulated homes that can be kept a comfortable temperature through far lower power radiators. These systems can be controlled in a way common to central heating systems, programmable to allow heat only in certain rooms and at certain times of day. Installing Direct Acting Electric Heating Systems to replace storage heaters in social high rises has reduced bills and allowed tenants to stop using back-up heat such as fan heaters.
Which has a page of impartial information on storage heaters.
Increased load
Electric heating systems in older buildings, multi-occupancy and high rise buildings face increased stress than a standard single-household building. When electrical systems were fitted in buildings dating from eg the 1970/80s and back, there was less overall demand on the electrical system than there is now. Increased use of power hungry domestic applicances together with wipespread use of multiple tech devices in the average home draw a great deal more electricity than would have been common in a house in the 1950s. Together with many older houses having poor insulation, an older building heated solely by electricity could become quite expensive to power.
Optimal use
As with the debate we referenced last week about gas heating, there is also disagreement about the best way to use electric central heating – keeping radiators turned off in unused rooms etc. Clearly it’s cheaper in simple energy bill terms not to heat a room that isn’t used, but could potentially-expensive damage be occurring to the fabric of the room? One argument in favour of the ‘always on’ approach is not wasting heat as a radiator heats and cools, but according to Robin Hood Energy,
“The energy expenditure require to maintain a steady temperature is greater than people assume, which is what makes the ‘always on’ option less efficient than it seems.”
Robin Hood Energy is an interesting organisation. On its website it describes itself as:
“Robin Hood Energy is the first not-for-profit energy company, owned by a local authority. We were set up to tackle fuel poverty and to help give people a cheaper, more helpful alternative to the Big Six. Launched by Nottingham City Council, we’re proud to be leading the way in trying to reduce fuel poverty for those who need help the most.”
Valves
Robin Hood Energy advises keeping as close a control over temperature in different rooms as your system allows. Often this is achieved by using valves – manual, thermostatic or smart. Manual valves are simply turned through a range of numbers like an oven dial – you stop when the valve is set to the temperature range you want for any given room. This controls how much hot water flows through and you are in charge.
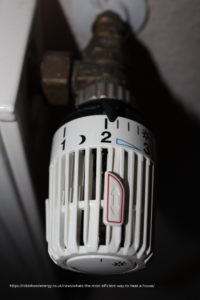
Thermostatic radiator valves, or TRVs, are set to the temperature you want the room to be. The system senses the temperature and opens or shuts the flow of hot water through the radiator accordingly. This has the scope to go haywire if your radiator is positioned in a cold or warm spot in the room or is influenced by other factors. If you’re considering fitting TRVs I urge you to read up on them, as much is said both in favour and against. The website boilerguide.co.uk has a page comparing different types of valves, and lists out what to consider with TRVs.
Lastly smart radiator valves. This connects to wifi and lets you control heating through an app. These can also connect with smart TRVs, in theory giving you close control of your heating wherever you may be.
Current electricity generation
So where does your electricity come from? Strides have been made recently in electricity generation in the UK, with renewable sources providing ever-increasing quantities of our power. A quick snapshot of power generation mid-morning on Tuesday 9th July shows that coal is producing zero energy, biomass 6%, solar, wind and hydro about 12%, nuclear 14%, and CCGT – combined cycle gas turbine – most of the rest. Business Green describes a combined cycle gas turbine as a system that:
“uses a gas turbine to create electricity and then captures the resulting waste heat to create steam, which in turn drives a steam turbine significantly increasing the system’s power output without any increase in fuel. The technology is typically powered using natural gas, but it can also be fueled using coal, biomass and even solar power as part of solar combined cycle plants.”
The National Grid describes its CCGT as powered by natural gas. At this moment we’re importing power from France and the Netherlands.

Green electricity
It’s possible for a household to source electricity from a company that uses only renewable energy, commonly referred to as green energy. We use this for all the workshop and admin processes that take place on our premises, and as a family firm we power our home with it too. E.On has just announced it will be providing all of its domestic customers on all tariffs with 100% renewable electricity, at no extra cost. This will affect about 3.3 million customers. E.On generates a proportion of the electricity it supplies, and has contracts with wind generating firms in the UK. The remaining requirement will be sourced from 100% green electricity.
This comes on the back of a survey of 4000+ electricity customers not currently on a renewable tariff. 61% said they would switch to green power if it was available at a reasonable cost. There are all sorts of offerings using various permutations of tariffs, renewable energy matching, green funds, nuclear-free and so on, so if you’re interested in using less fossil fuel and supporting renewables, read around carefully. There’s certainly plenty of information available but it really behoves you to read the samll print. Listen to this cautionary note from the Energy Saving Trust:
“Many green tariffs state that your supply is 100% renewable. Some companies buy a mix of renewable and non-renewable electricity, but make sure that the amount of renewable electricity they buy is at least as much as the amount they are selling to customers through their green tariff. A few companies only buy renewable electricity, and so all their customers are on a green tariff. In either case, all the renewable electricity produced is supported by Government schemes that require electricity suppliers to buy some renewable electricity, and so it is difficult to say how much extra renewable electricity is produced as a result of signing up to a green tariff, even if it is with a 100% renewable supplier.”
It goes on to make the invaluable point:
“Green tariffs are no substitute for energy efficiency and you should always do whatever you reasonably can to reduce your current use of electricity and other fuels before considering spending money on a green tariff.”
Cable.co.uk goes into detail about various suppliers on its website. There are quite a few, some long-established such as Ecotricity and many more much more recent. They have different visions and missions, so if you want to make the switch you should find a company that chimes with your financial and environmental priorities.
Electricity is a greener fuel, both in reality with fossil fuel use dropping in the UK, and in its potential, so from that point of view it is a preferable fuel to gas or oil. It’s usually simpler and cheaper to install than either gas or oil, with electric central heating less prone to problems than gas and without its inherent risks. If you’re in a position to pay the higher bills for electricity than gas, and particularly if your home is optimally insulated and draughtproofed, then electricity is likely to be the better option in most cases. For tenants and those reliant on storage heaters and/or pre-payment meters, the picture taken as a whole is less clear.
—
Insulation requirements for new builds
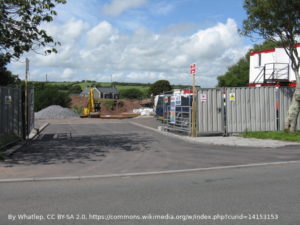
Building regulations exist to make sure that new buildings adhere to planning policy. In the UK this is carried out under the Building Act 1984 and the Building (Scotland) Act 2003, which affect new builds and aren’t usually retrospective. However regulations introduced in 2006 made it compulsory to upgrade energy efficiency in existing builds when extensions were built and certain other works carried out.
There was a total rewrite of the legislation in 2010, with numerous additions and amendments since, including some affecting measurement of energy and recognising the growing ways of heating and cooling buildings, imposing efficiency limits and requiring installation of energy use controls. Part L is titled “Conservation of fuel and power”. Kingspan Insulation explains insulation Building Regulations as follows:
“Building Regulations / Standards set the levels of thermal insulation required when carrying out building work, either for new build or refurbishment projects. These are expressed as a U-value which needs to be achieved. The required U-value will depend on the location of the project (England, Scotland or Wales), type of building (domestic or non-domestic) and the application (floor, wall or roof).” A low U-value is what you’re aiming for.
Wikipedia adds:
“Part L controls the insulation values of building elements, the allowable area of windows, doors and other openings, air permeability of the structure, the heating efficiency of boilers and the insulation and controls for heating appliances and systems together with hot water storage and lighting efficiency. It also sets out the requirements for SAP (Standard Assessment Procedure) calculations and carbon emission targets for dwellings.”
Zero carbon homes policy
Building regs specify minimum U-values, or heat transfer co-efficients, for building fabric. Tightening up of building regs means most new buildings will now include insulation, but this is a recent development. In 2016 there was a proposal to implement a “zero carbon homes” policy, first devised in 2007. The simple principle was that new builds wouldn’t make a net release of CO2. This would have had clear benefits to the householder in reduced bills, and to the environment with reduced emissions. First the proposals were watered down, then George Osborne scrapped them in the name of boosting housebuilding. According to an article on the ITV website, new build homes use more than twice as much energy to heat as a zero carbon home.
That was such a wasted opportunity to make a real difference, and begin our run-up to zero carbon that bit earlier. At the time the proposal was announced Britain was the only country making such a commitment. The proposals covered generating power on-site through renewable methods and implementing higher energy efficiency. Axing this proposal drew widepsread criticism from many quarters, including some closely involved in planning and housebuilding, who recognised what a step forward this would have been for the industry.
So how well do new builds perform?
Wikipedia describes UK insulation levels as low compared to the EU average. A study in 2004, admittedly a while ago now, claimed that 60% of new builds didn’t meet minimum standards, and of course any regulation is only as good as its enforcement. In 2006 a study for the Energy Saving Trust revealed that Building Control Officers often wouldn’t bother enforcing the rules on energy efficiency as it was considered low priority, but it would be nice to think that that figure would be far lower 13 years on.
In the summer of 2018, the government clarified that local authorities that wanted to could set higher energy efficiency standards than those laid out in part L of the building regs. It’s hugely encouraging that some councils want to set higher targets, and as usual, disappointing that the government won’t hold every council in the country to higher standards.
Despite this, improved building regs, building materials and methods, and a focus on energy efficiency, mean that a new build house is often going to be more energy efficient than an older one. Elmhurst Energy refers on its site to a Dept of Communities and Local Government report that shows 75% of new builds performing to A or B energy ratings, as opposed to 12% of non-new builds, but also notes a trend to slightly increasing energy consumption and CO2 emissions.
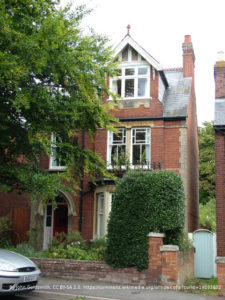
new-homes.co.uk, an online resource supported by the House Builders’ Federation, just to give you a flavour of their agenda, has an interesting set of pictures and figures on their site comparing a new build to a renovated Victorian property. Obviously these aren’t the only comparisons to be made, and energy efficiency far from the only considerations of the quality and comfort of the environment, but it does seem to show much better energy efficiency in the new build.
However this is very much the rose-tinted view of the energy efficiency of new builds. The CCC’s recent report, UK housing fit for the future, highlights the gap between how energy efficient new builds are designed to be, and how well they actually perform. Interestingly it calls for an immediate enforcement of current building regs, suggesting things maybe haven’t improved all that much since 2006.
It doesn’t take much searching online to find lots of stories of owners of new-builds unhappy with many aspects of their new homes. There have been court cases, silencing orders and much misery. There are numerous stories of poorly fitting doors and windows, cracks and even holes appearing in walls and ceilings. Imagine trying to keep a house in that state warm and dry. In some cases inspectors have deemed new builds unfit for habitation. It’s hard to see how, in the current climate, this sort of thing won’t happen more often as the government drives through building vast quantities of houses. We won’t name and shame here, but a quick search brings up frequent comments from people involved in the construction industry who are horrified at the poor quality of building.
There is talk of creating a new build ombudsman, but surely drawing up tighter standards and enforcing them would improve matters for the owners of new builds? An interesting article on website Mortgage Strategy covers just these issues, highlighting lack of competition within the housing industry doing nothing to drive up standards and highlighting significant levels of unhappiness among new build owners with an inadequate complaints and redress system.
Dry lining
An article in the Guardian in February this year discussed the problems with dry lining, which is responsible for chilly homes that are pricey to heat. Dry lining is the process of fitting ready-made plasterboard panels to walls, instead of having them plastered in the traditional way. Dry lining speeds up plastering from a matter of weeks to days. It’s commonly used in countries that experience far colder winters than the UK and is not in itself a problem.
However thermal imaging has revealed how poorly plasterboard is often fitted, having a negative impact on airtightness. The Guardian article points the finger of blame at pressure on housebuilders to build fast, so care and time aren’t taken over fitting the plasterboard. Cold spots appear between the plasterboard and the masonry, reducing thermal efficiency. This doesn’t happen in older buildings that had wet plaster applied, and is one case where modern new-builds make energy efficiency promises over older houses that don’t actually come to pass. Some pre-1900 buildings can be more airtight than 2006 building regs call for now.
To improve matters some developers fill gaps with mastic or decorator’s caulk, a filler that often sets fast and can be painted over, but it deteriorates and may be removed from skirting boards completely when carpet is fitted. In 2017 a research paper was released by Dr Jenny Love and colleagues from the UCL Energy Institute, which chewed data from nearly 150,000 homes tested under the Air Tightness Testing & Measurement Association scheme (ATTMA). It came up with similar findings, and made this comment:
““The result of meeting the target through temporary sealing, which fails after a short time, is that for most of a dwelling’s lifetime, air permeability will be higher than the design value”
Again this raises the crux of the matter, that the maximum potential energy efficiency is nowhere near being achieved in most new builds due to shortcomings in construction. A spokesman from the ATTMA equated the amount of air leakage modern building regs allow for to a hole the size of a 20p piece in every square meter of wall, which is nonsensical for any setting making a pretence to energy efficiency.
A large part of the problem with enforcing the building regs such as they are is that regulations allow for sample testing. This literally tests a sample of homes, not every one, so many problems are missed. The Guardian article suggests that airtightness testing is carried out by people not properly trained to do it.
ATTMA considers that builders have no incentive to spend the little extra required to build properly and to standards, as building regs are so minimal in this area and poorly enforced. The article describes several new build case studies where poor fitting has led to the house being cold, draughty and expensive to heat. In one case a house profiled actually exceeded airtightness regs when it was built, according to the builder. Even if that was the case, why does these buildings’ thermal performance deteriorate so fast? Clearly we still have it all to do in this country to make any meaningful difference in energy efficiency in private housing developments.
—
Energy efficiency in social housing
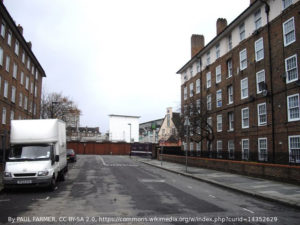
Social housing has traditionally been heated by electric storage heaters. Arguably the benefit of these has been felt more by the provider than the tenant, who is left with a clunky and hard-to-control heat source that they have little scope to change.
Decent Homes Standard
An article in Energy Manager magazine refers to the Decent Homes Standard, and holds it responsible for social housing providers leading the way with energy efficiency. According to the article poor housing is half as common in the social sector as in the private rented sector. The government has set high targets for the number of new social housing units required. The article quotes Martin Reed, MD of Elmhurst Energy who we referred to earlier:
““Social housing and local authority delivered about 33,000 homes in 2016/17, and therefore an increase to 150,000 a year for 20 years, to achieve the 3 million required, is a massive increase especially when you consider that the whole sector currently delivers approximately 280,000 homes. If the recommendation becomes reality, the house builders will need to build approximately 400,000 homes per annum, 42% more than today. What is important is that the mistakes of previous booms are not repeated. These new homes must be built to the highest standards of quality and energy efficiency to ensure that the future tenants don’t become the fuel poor statistics of the future.”
That’s very interesting given everything said just now about new builds’ real energy performance.
The Decent Homes Standard is described by wikipedia as “a technical standard for public housing introduced by the United Kingdom government”.
The four criteria for the housing are that it:
be free from any hazard that poses a serious threat to your health or safety
be in a reasonable state of repair
have reasonably modern facilities
have efficient heating and insulation
Clean Growth Strategy
A couple of years ago the government announced the Clean Growth Strategy as part of its efforts to meet its own targets set out in the 2008 Climate Change Act. Part of this is a target to get to get all housing up to Energy Performance Certificate (EPC) Band C by 2030. The government expects this to be achieved in part by increased uptake of renewable technologies but also replacing dirtier fossil fuels with cleaner ones. Broadly the Clean Growth Strategy has been positively received. Social housing has made improvements in energy efficiency and considered among the most energy efficient housing in the UK, but there’s massive scope to do more.
Of course this is constrained by the limits social housing providers can place on rents, but long-term budgets exist for upgrading properties. Social housing providers have long recognised that tenants not struggling to pay fuel bills are better able to keep up with the rent, so the economic case for energy efficiency is made. Grants and programmes exist to support social housing improvement, especially to improve the worst performing stock. Although feed in tariffs have been hit recently, incentive schemes have prompted providers to install solar panels. At scale, this is still worth it.
Energiesprong
Long term, housing will need to hit better than band C for energy efficiency. Social housing providers could get ahead by improving to better than band C from the off, especially given that they will own their housing stock for many years to come. Aiming for zero carbon is a lot to ask, but makes a great deal of sense. One way to achieve this is through Energiesprong. Energiesprong is a combined funding and building model that describes itself thus:
“Part of the innovation is how the works are funded. The household pays an ‘Energy plan’, and the landlord (NCH) receives an on-going income to fund similar works to more homes. The resident has a much more comfortable home, and a flat rate cost for energy, which will not rise significantly when energy bills rise.”
Crucially it guarantees that the work will perform as advertised, something the regular UK construction industry is signally failing to do just now. Work takes place in just a matter of days, and has been put into practice in the British social housing sector. The work comes with a 30 year warranty. Energiesprong works in many countries including the Netherlands, where it has been particularly successful, the USA, France and Germany.
A number of projects have taken place in the UK, including retrofitting 10 homes in Nottingham as a pilot. The homes were wrapped in a prefabricated wall with solar panels on top. This is part of a wider approach by Nottingham council to improve energy efficiency in its properties across the city. London, Essex and Devon all have plans for Energiesprong works.
In Scotland social housing providers must abide by the Scottish Government’s Energy Efficiency Standard for Social Housing (EESSH), meeting its standards by 2020. Using the Energy Efficiency Hierarchy method, providers look at the right solution for a house or flat by first assessing the property for fitting cavity, internal or external insulation to reduce energy needs, fitting new energy efficient heating system to use energy more efficiently, and lastly fitting renewable energy technologies such as PV panels.
Energy efficiency refurbishment
In Norwich a development of 105 passivhaus homes has been built. This is one of the largest energy efficient schemes underway in the UK. A report on the Science Direct website highlights great potential to improve energy efficiency in social housing in emerging countries such as Brazil. Emerging countries have a high energy demand, which energy efficiency in social housing would help to reduce. In Denmark the Frederikshavn Housing Association in northern Denmark is refurbishing nearly 300 homes to a high energy efficiency standard. It’s also investing in renewable technologies integrated into the building. Their target is a 30% energy saving. They’ll achieve this through improving the building envelope, using less energy hungry lighting systems, fitting HVAC and upgrading windows, and providing tenants with smart energy monitoring systems.
A report from the Department for Business, Energy and Industrial Strategy looks at the barriers to retrofit in social housing. It found that moneys for these works are separate from the routine maintenance budget. As each has different contracts set up to deliver, it can be difficult to co-ordinate works. Ignorance is another problem. A great idea on paper can meet problems on the ground when a housing provider or its suppliers don’t really grasp the detail of what’s required. Limits on funding and staff cuts pose more problems. Both of these issues push energy efficiency retrofit behind more urgent works such as bathroom and kitchen replacements. The report is available as a PDF download and is food for thought.
Essentially, upgrading social housing to or beyond the minimum standards required is a win for the tenant. It also protects the landlord’s investment. However it costs money, and the research and planning time must be prioritised by the provider if much is to change beyond a handful of exciting projects.
—
Energy saving product of the week
This week we’re looking at saving power in the office. If you’re already keeping your phone charged with a solar charger, you can team that with a solar-powered keyboard. Logitech is the main manufacturer of these. The K750 has PV cells on its top edge and will charge in sunlight or artificial light whenever it detects it; you don’t have to think about topping up the charge. The keyboard makes various other claims about being wonderful which is great as it retails from Logitech for £80.
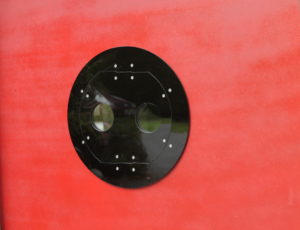
What are we up to? We delivered new Petflap stock to the warehouse last week and are now working on new regular stock and special orders. We’ve had part of our photo shoot, with more to come over the next week or two. We’re looking at better ways of creating our trunking and progressing with a third party to keep up a steady stream of parts. We’re happy to answer as many pre-purchase questions as anyone can ask. Don’t hesitate to get in touch if you have a Petflap query.
Thank you for listening to episode 6 of the Energy Efficiency Podcast, available through Apple Podcasts. If you like your podcasts with pretty pictures, a video version is available on YouTube – look for the Ecoflap channel where we also have product videos. Until next time you can find us on both Twitter and Instagram as Ecoflap, and on Twitter we also tweet under The Petflap In next week’s episode we’ll look at ground source heat pumps, energy efficiency in the leisure sector, and passive cooling. Bye.
Music credit: “Werq” Kevin MacLeod (incompetech.com)
Licensed under Creative Commons: By Attribution 3.0 License
http://creativecommons.org/licenses/by/3.0/