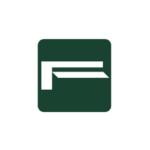
Coffee
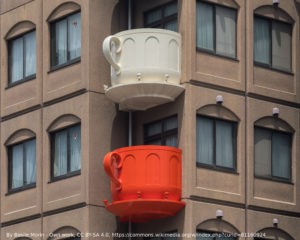
Welcome to Coffee: The Energy Efficiency Podcast – episode 23, the podcast that brings you a mix of energy efficiency news, and developments all year round. You can find us on both Twitter and Instagram as Ecoflap, and on Twitter we also tweet as The Petflap.
We’re now taking reservations for Petflaps ready by mid-March. Please email info@ecoflap.co.uk to reserve yours. We’re having reports of great results on Shetland, where no cat flap has previously stood up to the job. As our now repeat customer says, if it works on Shetland, it will work anywhere!
Next time: wooden buildings, energy efficiency in wine production, and the councils demand more money from government for energy efficient homes.
Ft articles:
- Diesel and petrol vehicle sales ban
- Coffee waste as biofuel
- Energy for Londoners
- Episode 6 – Energiesprong
- EU energy positive projects
- +CityXChange
- Efficiency for Access webinar
- Historic building energy efficiency renovation webinar recording
Energy efficiency in coffee production
Coffee is produced in more than 70 countries, the majority of them in the equatorial regions of the Americas, Southeast Asia, the Indian subcontinent, and Africa, overwhelmingly developing countries where about 25 million smallholders dedicate themselves to coffee. The process from bean to cup generates enormous volumes of by-products and residues, so keeping the black stuff flowing requires scrutiny and improvement of the sustainability of its production.
Processing coffee beans is energy-intensive, with roasting alone responsible for up to 80% of a coffee processor’s power consumption. The costs of that energy can be the difference between running a business at a profit or a loss. Providing energy for coffee processing could therefore be seen as an obstacle, but it also provides an opportunity for energy efficiencies and innovation.
In the Caribbean, the USDA’s Natural Resources Conservation Service (NRCS) is offering financial assistance to encourage procuders to upgrade from traditional and inefficient drying methods to newer, more efficient methods. The EQIP Energy Initative helps processors migrate to highly efficient new technologies, saving energy and the associated costs, and reducing their use of fossil fuels. One example of machinery that the NRCS is aiming to consign to history is the ‘batea’. A batea is a rotational dryer used for drying the coffee beans after the coffee bean has been removed from its exterior skin and gel layer (the “wet mill” stage). Typically these bateas are made from scrap parts from trucks and other machines, including truck transmissions and engines. Many run on diesel but some use electricity. Bateas tend to be much bigger than they need to be, using blowers originally designed for use in a silo, so they generally use about three times as much electricity than is needed to dry the single layer of coffee beans inside the batea. The rate of drying is hard to control in a batea, so often beans have roasted before they’ve dried properly.
Bateas need to be replaced by a purpose-designed silo-type dryer, that are the right size for coffee drying and designed for uniform drying. These silos reuse the heat from the main dryer bed and pipes it back through a pre-drying layer, and it has just one motor. Much better drying is achieved with a lot less energy expended. A silo of this type will use just 10% of the energy of a batea run on propane gas.
Pruning coffee trees generates a great deal of stem waste. Coffee stems are well-suited to use as a solid fuel, as they have a high lignocellulose content, a low calorific value and a low ash content. Research has looked at their suitability for power generation in the Colombian coffee industry which could then power the drying stage. It could also be used to provide domestic power to those who work in the coffee industry. At the moment the stems are burnt in the fields or used very inefficiently as solid fuel in domestic stoves. To quote from the paper:
“An analysis of the energy demand and coffee stems availability within the Colombian coffee sector shows that the biomass production level in medium- to large-scale coffee farms is well matched to their energy demands, offering particularly attractive opportunities to deploy this bioenergy system.”
Beyond the stems, husks and pulp from the wet mill can be used as silage and compost. Various elements of the coffee resides work well as biomass and in the production of biogas and bioethanol. Grounds work well in compost (that’s where all ours go) and as a substrate for mushroom growing. Colombia relies heavily on hydropower for its renewable energy, and it provides 65% of the country’s total power requirements. Biomass could make a significant contribution in Colombia. It would also bring power to more remote areas and help to make the energy supply more reliable.
Buhler Group manufactures food processing equipment and is aiming for top-end efficiency in water and energy use, and minimum waste. In partnership with Norwegian coffee producer Joh Johannson it is creating the most environmentally-friendly coffee processing plant in the world. As well as employing highly efficient machinery and using heat recovery from roasting to heat the building and other processes, the plant will run off biogas and huge solar cells automatically managed for optimum performance. Potentially the plant will produce more energy than it uses.
Curiously, scientists at UCLA have discovered that caffeine can make perovskite solar cells more efficient at converting light to power. Perovskite is a type of mineral and materials made from it are typically easy and cheap to manufacture. Perovskite solar cells have improved massively in efficiency recently but the search was still on the boost the cells’ efficiency and their stability long-term. Adding caffeine into the mix allowed the perovskite to react with much less energy and increased its resistance to heat, meaning the solar cells would be less liable to heat damage.
Overwhelmingly the coffee industry is concerned with climate change, particularly with respect to water supply, biological threats to the coffee trees, and the numbers of small coffee growers who are packing up shop. Article after article focussed on increasing yield and reducing the gap between wealthy coffee roasters and poor coffee growers. Remarkably little is written about improving the energy efficiency of the coffee industry.
Music credit: “Werq” Kevin MacLeod (incompetech.com)
Licensed under Creative Commons: By Attribution 3.0 License
http://creativecommons.org/licenses/by/3.0/